
„We will no longer structure the series based on length, size, and width, but rather on the status of the electrical system. In the future, the nature of the electrical system will be more important than the hardware, meaning the automobile itself.“
Harness Packaging: durable, tear-resistant, and robust.
Wiring systems are the nervous systems of a car. They distribute the signals from sensors and control units.
Assembly requires a very high degree of care and caution to prevent damage. The iba harness packaging has been proven tools for all well-known car manufacturers for decades. Threaders, pouches, and wrapping cloths from IBA assist with the quick and safe installation of wiring systems. In complete custom-made, they facilitate the installation of arm-thick cable strands – around all corners and edges.
Our harness packaging is durable, tear-resistant, and robust. They can withstand quite a bit. This is ensured by threading aids, assembly bags, and structure bags. We use abrasion-resistant and ESD-capable* materials such as ESD-Tech and Multifil. With Multifil, we even achieve 750,000 Martindale test abrasion cycles. We also use cotton, mesh, and our developments.
Fit and protection in particularly hard-to-reach places are the top priority for wiring harness packaging. We know that – and produce your harness casing solution according to your individual requirements.
*ESD, Electrostatic Discharge
The 3 steps to your cable harness encasement:
Your requirements:
Is easy, quick access to the content important? Which bag contents should be particularly protected? Accordingly, our recommendation varies for the model of the harness, the layout of the bag interior, the positioning of exterior pockets, etc.
What are the suitable materials? Should the surfaces be smooth and frictionless to handle on the line, or is an ESD material recommended to protect the electronic components? Of course, both are possible.
And last but not least: Which closure options will be used?
We are happy to consult with you and develop the perfect harness packaging which can exactly meet your needs.
The practical test:
Only reality counts! Even the most sophisticated testing methods cannot replace a user/application test under real conditions. This is the main reason why we work with 1:1 prototypes, designed and produced in IBA Hartmann’s prototyping by our master fine bag maker. The prototypes correspond 1:1 to the samples of the subsequent series production.
Now, it’s time to confront the harness packaging with all the adversities it will encounter during its lifetime. We are happy to take the necessary time for this. Ultimately, you decide which details need to be improved for the series. In the end, we will jointly develop your perfect packaging.
Production:
According to the technical specifications, the agreed budget, your schedule, and the required quality certificates, your harness packaging will be manufactured by one of our partners in Asia, Europe, or Germany.
These are your advantages with iba hartmann TASCHEN:
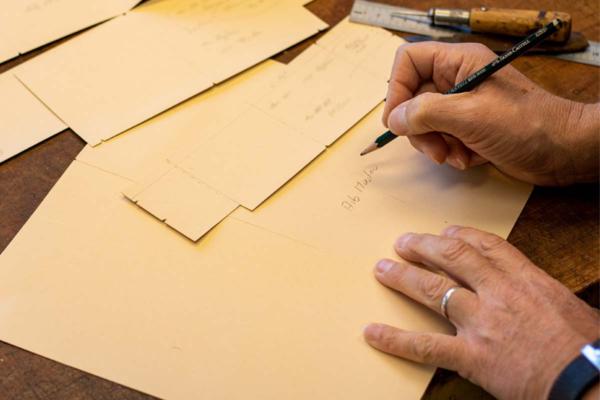
Custom harness casing solutions,
developed by professionals.
We develop technically sophisticated wiring harness packaging systems. Thanks to our many years of experience with harness packaging, we are able to show you thoughtful solutions in detail. This way we simplify the handling of our solution. You are welcome to learn more in person on site or during your visit to our prototype workshop “Prototyping”. In a conversation with our master fine bag maker at IBA Hartmann in Augsburg, you can clarify all details.
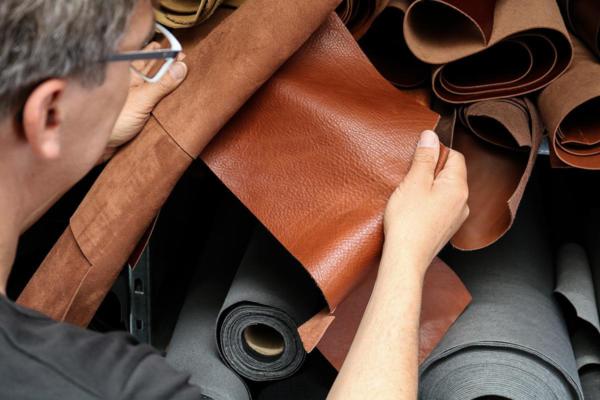
DIN ISO 9001:2015 certified.
As one of the first companies in our industry, we have been certified according to DIN ISO 9001 since 1996. This way you can be sure that all project steps are equally orderly, transparent, and standardized. Our QMB (Quality Officer) always keeps an eye on everything running according to the ISO requirements. Thus, our high production quality is consistently ensured – during product development in-house and during the production process at our partners’ locations.
You can trust that your serial production will be realized piece by piece in constant quality. If desired, we record further test criteria through QMB checks at our manufacturing sites.
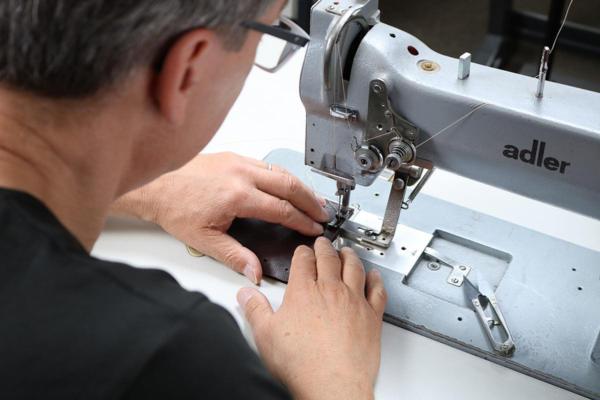
Cable harness encasement only in custom-made.
Reissues of wiring harness packaging are important for IBA Hartmann because we are not only pleased with your vote of confidence when you place a repeat order for a previously produced harness packaging system. We always seek direct, intense exchange with you at this opportunity because we want to learn and improve: Your input from everyday practice is of particular importance to us.
Now we get the chance to go one better. We want to know where potential weaknesses have occurred in everyday life, which exterior pockets should be positioned better, which closures close easier, or which areas are particularly exposed. You can play it safe: We will not rest now. We will keep developing.